Services - Pillar Bedding
LongRifles Inc. is committed to delivering pillar bedded stocks unmatched in the custom rifle industry. Our approach creates an accurate, durable casting of the receiver with special emphasis on final presentation. We encourage our clients to disassemble their rifles and inspect the interior, as we feel this is a direct reflection of the overall presentation.
We use a resin system designed for commercial boiler repair with very good adhesion, high compression and shear tolerance, chemical resistance, and very, very low percentage of shrinkage while curing."
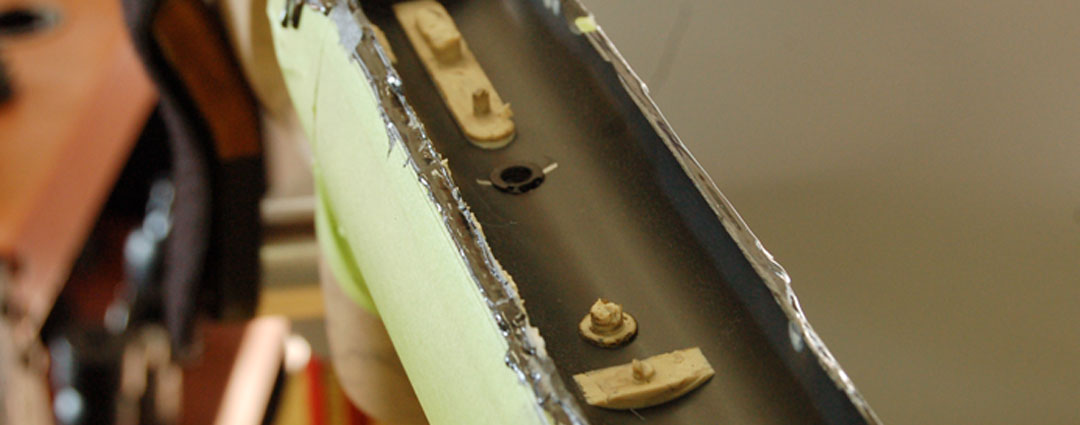
The use of pillars has become an almost standard practice when accurizing a rifle. Intended to resist the compressive forces by the action screws, they are commonly made from either aluminum or steel. Our pillars are made from 300 series stainless as it has superior corrosion resistance. They are uniquely profiled to ensure precise positioning of the action in the stock while maintaining a uniform film thickness of bedding.

Every bedding operation begins with the receiver’s external features carefully measured and documented on a build sheet. We use inspection equipment common to industries like aerospace for this kind of work. This step is critical as it ultimately directs the whole process.
The build sheet drives a 3 dimensional computer model that directs the machinery to inlet the rifle stock. Every gun we build is done this way ensuring not only an accurate casting, but a uniform film thickness of bedding.
The “Primary Inlet” is a term we use to describe removing material where the action is going to reside. All resin systems experience a degree of shrinkage as a natural byproduct of the chemical reaction that takes place as it hardens. Since this cannot be eliminated the solution we’ve found to work best is controlling the film thickness between the stock and the receiver to manage distortion while curing.
The use of CNC equipment necessitated designing and manufacturing our own special fixtures. This ensures rigid and accurate work holding of the rifle stock in the machining center. This adaptive set up allows for virtually any stock configuration.

Once the stock is machined it’s then masked to protect the exterior finish. Again this is done very carefully to ensure resin only adheres where it’s supposed to. A successful bedding job depends on detail oriented preparation work.
The action is now packed with clay specifically intended for bedding and blended to the receiver contour. Every feature is masked this way with seamless transitions to ensure an accurate casting while eliminating the risk of accidently gluing the receiver in the stock. Once completed, a film of release agent is applied to the metal parts. We use a commercial mold release agent designed to work with an ultra thin film thickness, further ensuring the accuracy of the casting.
Resin is carefully proportioned and mixed in a manner that minimizes the introduction of air bubbles, while ensuring that the two base components are fully blended. This promotes an even hardness, cure rate, and a dependable service life. A “slow cure” of 24 hours in a controlled environment further helps to manage shrinkage.
Once cured the action is removed from the stock. In some ways this is the most critical portion of the whole bedding process as the edges are very delicate and easily damaged. If this happens the job is scrapped and started over. Exceptional stock work depends on clean lines and seamless transitions. It’s something we strive for in every gun we build. A student mind approach has lead to some innovative tools that aid the job tremendously. This is our “action jack.” It lifts the receiver straight out of the stock eliminating the possibility of the recoil lug damaging the bedding from rocking motion.
With the receiver removed all that remains is a visually clean, accurate casting free of surface inclusions like air pockets, swirl marks from wax base release agents, and voids from resin flowing into unwanted features.
Laminate wood stocks and the gel coats used in many synthetics are very susceptible to chips and flakes. Extensive research for the best tooling helps ensure the integrity of the stock remains at every step of the build. Crisp lines and well defined corners are what we strive for.
Features like the trigger well are individually fitted and kept conservative to preserve as much of the original stock as possible. Internal corner features are machined with a radius to resist chips and flaking.
The unique pillar design allows for the screw holes to be spot faced while still providing direct support to the receiver. This ensures the action screws can never damage the bedding and that resin never flakes or chips away from the pillar bore from being too thin.
The bottom of the stock receives the same kind of treatment. Having to cast or “bed” the floor metal is avoided by using multi-axis computer controlled tool paths that machine a 1:1 inlet in the stock.
Performance is unaffected and the final presentation is much cleaner.
Final inspection is both technical and visual. The technical portion involves measuring the amount of deflection between the stock and the barreled action. With the action screw torque at 40 inch pounds and individually released, deflection is measured with an indicator mounted to the barrel and the stylus contacting the forend of the stock. A properly bedded rifle will typically show a deviation of less than .001” on the front screw and less than .0005” on the rear.
The visual portion is as simple as asking, “does this look right?” Are the machined features clean in appearance? Is the casting free of inclusions like air bubbles and voids? If the answer is yes then the bedding is completed.
At this point the rifle begins to take on its identity. Application and customer needs decide the ultimate outcome.